プラスチック射出成形は、プラスチック成形の中で最も広く使用されているものです。プラスチック射出成形部品は、電子、電気、電気、医療、輸送、自動車、照明、環境保護、セキュリティ、家電製品、スポーツ用品、その他の産業や製品に使用されています。
射出成形とは何ですか?プラスチック射出成形は、完全に溶融したプラスチック材料をスクリュー攪拌し、冷却および硬化した後、金型キャビティに高圧射出して成形方法を取得することにより、特定の温度範囲で部品を製造する製造プロセスです。この方法は、複雑な部品のバッチ生産に適しており、重要な処理方法の1つです。金型の閉鎖、溶融プラスチックの射出、圧力の維持、冷却、金型の開放、製品の取り出しの6つの段階があります。速度、圧力、位置(ストローク)、時間、温度は、射出成形の5つの重要な要素です。
注射生産ユニットの3つの要素
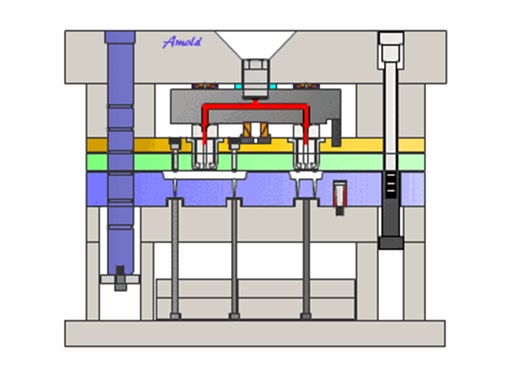
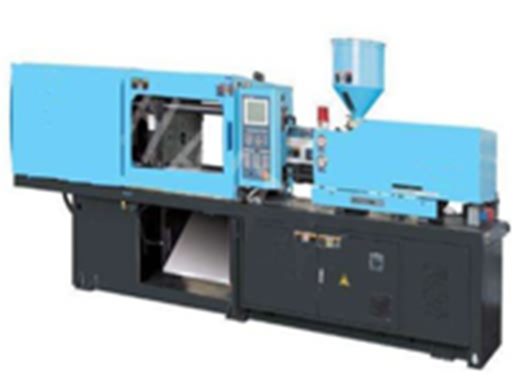
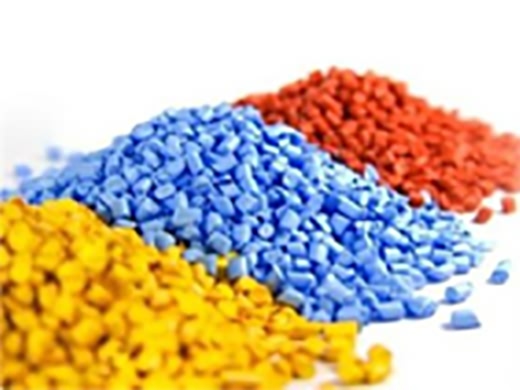
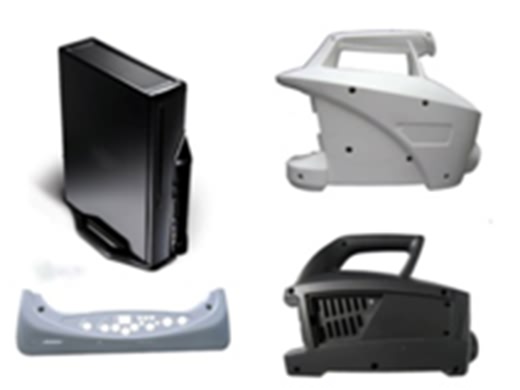
射出成形製品の用途
(1)電子製品の場合:。通信電子製品および家庭用電化製品(プラスチックハウジング、エンクロージャ、ボックス、カバー)携帯電話、ヘッドホン、テレビ、テレビ電話、POSマシン、ドアベル。
(2)家電製品:コーヒーメーカー、ジューサー、冷蔵庫、エアコン、ファンウォッシャー、電子レンジ
(3)電気機器:電気メーター、電気ボックス、電気キャビネット、周波数変換器、絶縁カバーおよびスイッチ
(4)医療およびヘルスケア機器および装置:無影灯、血圧計、注射器、スポイト、薬瓶、マッサージャー、脱毛装置、フィットネス機器
(5)自動車の場合:ダッシュボードボディフレーム、バッテリーブラケット、フロントモジュール、コントロールボックス、シートサポートフレーム、スペアプラセンタ、フェンダー、バンパー、シャーシカバー、防音壁、リアドアフレーム。
(6)産業機器:機械計器盤、ギア、スイッチ、照明。
(7)交通機器および車両機器(ランプカバー、エンクロージャー)信号ランプ、標識、アルコールテスター。
注射生産ユニットの3つの要素
金型、射出成形機、プラスチック原料が射出成形の基本単位です。金型と射出成形機が生産設備であり、プラスチック原料を使用して製品材料を構成しています。
1.射出成形金型
射出成形金型は、プラスチック製品を製造するための一種のツールです。また、プラスチック製品に完全な構造と正確なサイズを与えるためのツールでもあります。射出成形は、いくつかの複雑な部品のバッチ生産で使用される一種の処理方法です。具体的には、溶融プラスチックを射出成形機により高圧下で金型キャビティに射出し、冷却硬化後に成形品を得る。射出成形金型は、金型構造、製品設計要件、製造モード、設置および使用モードに応じて、さまざまなタイプに分類できます。
金型の製造コストは高いが、耐用年数が長く、生産効率が高いため、通常は大量生産にのみ使用されます。プラスチック部品の量産には射出成形金型を使用しています。多数の高効率プラスチック製品は、金型製造のコストを大幅に共有しているため、単一製品の射出成形の製造コストは、他の処理方法よりもはるかに低くなっています。金型設計と金型検証には3つの段階があります。
(1)金型設計:
金型設計は、製品設計、設計ソフトウェアの使用、機械加工の金型製造レベルおよび射出成形プロセスの特性、金型メカニズム全体の設計、部品に基づいています。
(a)最初のステップはプラスチック製品の設計を分析することです
(b)2番目のステップはダイ材料の選択です
(c)3番目のステップは金型メカニズムの設計です
(d)4番目のステップは金型部品の設計です
(2)金型加工
金型加工は、主に機械加工を経て完成します。図面レビュー→材料準備→加工→金型ベース加工→金型コア加工→電極加工→金型部品加工→検査→組立→フライング金型→トライアル金型→製造
射出成形金型の処理サイクルは、金型の複雑さと処理レベルによって異なります。一般的な生産サイクルは20〜60営業日です。金型加工に使用される機械:CNC、旋盤、一般フライス盤、表面研削盤、EDM、WEDM、および手工具、測定工具などの組み立て
(3)射出成形金型の種類:
射出成形金型は、金型構造、製品設計要件、製造モード、設置および使用モードに応じてさまざまなタイプに分類できます。
(a)2プレート金型:射出成形では、金型の可動金型と固定金型を分離し、プラスチック部品を取り出します。これは、ダブルプレート金型とも呼ばれます。非常にシンプルで基本的なプラスチック射出成形金型です。必要に応じて、シングルキャビティ射出成形金型またはマルチキャビティ射出成形金型として設計できます。広く使用されている射出成形金型です。シングルまたはマルチキャビティ射出成形用の金型、
(b)3プレート金型:ダブルパーティング金型とも呼ばれます。ワンピースの外部射出成形金型と比較して、デュアルスプリット射出金型は、ポイントゲート金型の固定金型コンポーネントに部分的に移動可能なストリッパーを追加します。構造が複雑で製造コストが高いため、一般的に大型部品の金型には使用されません。
(c)ホットランナー金型:ホットランナー金型とは、加熱装置を使用してチャネル内の溶融物を常に固化させない金型を指します。従来の金型製造よりも効率的で、原材料の節約にもなるため、今日の工業先進国や地域ではホットランナー金型が広く使用されています。ホットランナーシステムは、一般的な金型よりもホットランナーシステムが1つ多いため、コストが高くなります。
(d)2色金型:一般に、同じ射出成形機の射出成形、2成形で、2種類のプラスチック材料と呼ばれますが、製品の金型は1回のみです。一般に、この成形プロセスはダブル射出成形とも呼ばれ、通常は金型のセットで完了し、特別な2色射出成形機が必要です。
(4)射出成形金型の施工サブシステムは以下のとおりです。
射出成形金型は通常、次のサブシステムで構成されています。
(a)ゲートシステム。これは、射出ノズルからキャビティまでの金型内のプラスチック流路を指します。一般的なゲートシステムは、スプルー、ディストリビューター、ゲート、コールドホールで構成されています。
(b)サイドパーティングとコアプルメカニズム。
(c)誘導メカニズム。プラスチック金型では、主に特定の側圧を位置決め、ガイド、および支持する機能を備えており、金型の移動と固定の正確な閉鎖を保証します。ダイクロージングガイド機構は、ガイドピラー、ガイドスリーブまたはガイド穴(テンプレート上で直接開いている)、および位置決めコーン表面で構成されています。
(d)排出/離型メカニズム。押し出しとコア引き抜き機構を含みます。主に金型から部品を取り出すために使用されます。エジェクターロッドまたはパイプジャッキまたはプッシュプレート、エジェクタープレート、エジェクターロッド固定プレート、リセットロッドおよびプルロッドで構成されています。
(e)温度制御システム。冷暖房装置。
(f)排気システム。
(g)成形部品とは、金型キャビティを構成する部品を指します。主に、パンチ、雌型、コア、成形ロッド、成形リング、インサートが含まれます。
(h)固定および取り付けられた部品。。
(5)金型の材質
プラスチック金型には、熱可塑性金型と熱硬化性プラスチック金型が含まれます。プラスチック金型用鋼は、強度、硬度、耐摩耗性、熱安定性、耐食性などの特性が求められます。さらに、熱処理の小型化、加工性能の向上、耐食性の向上、研削および研磨性能の向上、補修溶接性能の向上、粗さの高さ、熱伝導率の向上、加工のサイズと形状の安定性など、優れた加工性も求められます。条件。
射出成形金型に使用される射出材料の種類は、金型鋼の選択に大きな影響を与えます。ガラス繊維などの補強剤や改質剤を添加した場合、金型へのダメージが大きいため、材料の選定を総合的に検討する必要があります。強酸性プラスチック材料は、PVC、POM、PBTです。弱酸プラスチック材料は、PC、PP、PMMA、PAです。一般に、S136、1.231、6420およびその他のモールド鋼は、強腐食性プラスチックに選択されますが、S136、1.2316420、SKD61、NAK80、pak90718などは弱腐食性プラスチックに選択できます。製品の外観要件も、金型材料の選択に大きな影響を与えます。透明部品および鏡面研磨の製品の場合、使用可能な材料はS136、1.2316718、NAK80、およびpak90420です。透明度の高い金型はS136、次に420を選択する必要があります。価格とコストを考慮せずに製品要件を満たすだけの場合は、優れた設計者ではない可能性があります。金型の製造コストも最優先事項です。
2.1射出成形装置
(1)。射出成形機:
プラスチック成形金型により、熱可塑性または熱硬化性プラスチックをさまざまな形状のプラスチック製品に加工するための主要な成形装置です。水平射出成形機、垂直射出成形機、2色射出成形機、全電気射出成形機ただし、どのような種類でも射出成形機、その基本的な機能は2つです。
(a)プラスチックを加熱して溶かします。
(b)溶融プラスチックに高圧をかけ、キャビティを排出して充填します。射出成形機の主なパラメータは、クランプ力、最大射出量、最大および最小金型厚さ、移動ストローク、プルロッド間隔、射出ストローク、および射出圧力です。さまざまなサイズ、構造、材料の部品、およびさまざまなサイズとタイプの金型の場合、射出成形機のさまざまなモデルとパラメータを選択する必要があります。フル電動射出成形機には、射出速度が速く、制御が正確で、生産効率が高いという利点があります。一部の精密部品の射出成形に使用されます。
(2)補助装置:
(a)射出成形機のマニピュレーターは、人間の上肢の一部の機能を模倣し、自動的に制御して製品を輸送したり、所定の要件に従って工具を操作したりできる自動生産装置です。マニピュレータは、操作サイクルの一貫性を確保し、品質を向上させ、安全性を高めることができます。中国のプラスチック加工産業の急速な発展に伴い、射出成形装置の自動化の度合いはますます高まっています。最新の射出成形機には、生産効率を向上させるためにマニピュレーターが装備されていることがよくあります。
(b)オイルヒーター/ウォーターチラー:金型を流れる液体による加熱または冷却、金型温度の上昇、表面品質の向上、または金型温度の急激な低下による生産性の向上。
(c)除湿乾燥機:加熱およびブローによりプラスチック材料から水分を除去します。
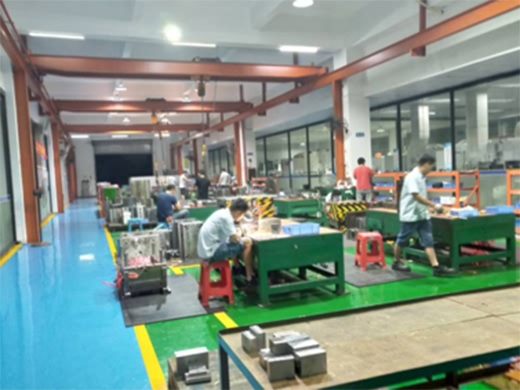
射出成形ワークショップ
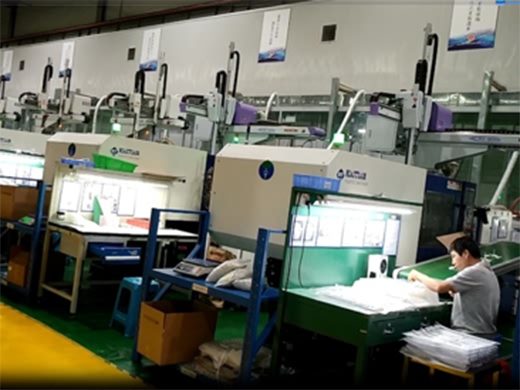
射出成形生産ライン
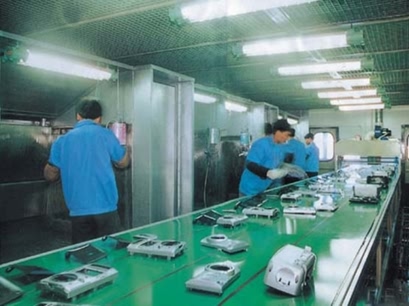
プラスチック部品塗装ライン
3.プラスチック材料
射出成形で使用されるプラスチック樹脂:射出成形で使用される最も一般的な熱可塑性樹脂は次のとおりです。アクリロニトリルブタジエンスチレン、アクリロニトリルブタジエンスチレン(ABS)は、不透明な熱可塑性でアモルファスのポリマーです。...ポリエチレン。...ポリカーボネート。...ポリアミド(ナイロン)...耐衝撃性ポリスチレン。...ポリプロピレン
素材 | 密度 | 型 収縮 |
特徴 | 応用 |
グラム/ cm3 | % | |||
ABS(アクリロナイトライトブタジエンスチレン) | 1.04〜1.08 | 0.60 | 安定したサイズ、優れた包括的な機械的特性、簡単な電気めっき、簡単な射出成形 | 電子製品用のプラスチックハウジング |
PC(ポリカーボネート) | 1.18〜1.20 | 0.50 | 優れた衝撃強度、安定したサイズ、優れた断熱性。耐食性と耐摩耗性が悪い | プラスチックハウジング、保護カバー、 電子製品、電気製品用の小型トランスミッション部品 |
PMMA(ポリメチルメタクリレート) | 1.17〜1.20 | 0.60 | 92%の優れた透過率と優れた総合的な機械的強度を備えています。ノッチ衝撃強度が低く、割れを強調しやすい | 計器の透明レンズとディスプレイダイヤルアイコン |
PP(ポリプロピレン) | 0.89〜0.93 | 2.00 | 収縮性、耐湿性に優れ、耐熱性があり、破れにくいです。低耐摩耗性、 経年劣化しやすく、低温性能が悪い | 食品容器、食器、 電子レンジボックス、医療容器 |
(塩化) | 1.38-1.41 | 1.50 | 丈夫で耐摩耗性があり、優れた断熱性、より困難で貧弱な高温性能を形成する | パイプとプロファイルの作成 |
ナイロン | 1.12〜1.15 | 0.7-1.0 | 硬く、耐摩耗性、耐水性、 耐疲労性、優れた断熱性。高収縮、方向性 | 機械部品、化学部品、 トランスミッションパーツ |
POM(ポリアセテル) | 1.42 | 2.10 | 優れた機械的特性、 高い強度と硬度、耐摩耗性と耐衝撃性。熱安定性が悪い | 機械部品、化学部品、 室温で作動するトランスミッション部品、摩擦部品、トランスミッション部品 |
TPU(熱可塑性ポリウレタン) | 1.05〜1.25 | 1.20 | エラストマー、耐摩耗性、耐油性、 高温および低温の弾力性、無毒 | 医療、食品、 電子製品と低温環境 |
射出成形プロセスは、溶融した原材料を加圧、射出、冷却、分離して、特定の形状の半製品を製造するプロセスです。プラスチック部品の一般的な射出成形プロセスには、主に7つの段階があります。:パラメータ設定->型閉->充填->(ガスアシスト、水アシスト)圧力維持->冷却->型開->離型。
速度、圧力、位置(ストローク)、時間、温度は、射出成形プロセスの5つの重要なパラメーターです。射出成形の生産では、主にこれらのパラメータをデバッグして、適切なサイズと外観を改善および取得します。
7つの典型的な射出成形技術
1.ダブル射出成形
2.オーバーモールド射出
3.ホットランナー射出成形
3. IMD:インモールド装飾射出
4.大きな部品の注入
5.ハイライト部品の射出成形
6.自動車部品の射出成形
7.薄肉部品の射出
後処理
プラスチック射出成形部品は、さまざまな標準射出成形可能ポリマーで、必要な0.1グラム〜10kgの体積で提供できます。さらに、ねじ込みインサート、金属フレットコネクタ、またはその他のプラスチック射出成形部品を過剰成形して、製品をプロフェッショナルな仕上がりにすることができます。サブアセンブリは、プラスチック射出成形サービスの一部として作成し、要件に合わせてパッケージ化することもできます。同じことが、次のようなさまざまな仕上げプロセスにも当てはまります。
*プラスチックのクロムメッキ
* ペインティング
*デジタルイメージング
* パッド印刷
* RFシールド
*パッケージングとスティラージ
*射出成形の品質管理当社は、迅速な金型、プロトタイピング、および成形後のサービスも提供しています。
成形不良とトラブルシューティング
成形後、プラスチック部品と所定の品質基準(検査基準)との間に一定の違いがあり、次のプロセスの要件を満たすことができません。これはプラスチック部品の欠陥であり、品質問題と呼ばれることがよくあります。これらの欠陥の原因を調査し、最小限に抑える必要があります。一般的に言えば、これらの欠陥は次の側面によって引き起こされます:カビ、原材料、プロセスパラメータ、機器環境および人員。
1.一般的な欠陥:
(1)。色差:射出成形部品の色が肉眼で単一の標準色サンプルと異なる場合、標準光源下での色差と判断されます。
(2)。充填不足(接着剤不足):射出成形部品が充填されておらず、接着剤不足と呼ばれる標準テンプレートに適合しない気泡、ボイド、収縮穴などがあります。
(3)。反り変形:プラスチック部品の形状は、離型後または後の期間で回転およびねじれます。真っ直ぐな面が内側または外側を向いている場合、または平らな部分に上下がある場合、製品の脚が等しくない場合、それは変形と呼ばれ、局所的な変形と全体的な変形に分けることができます。
(4)。ウェルドラインマーク(線):金型内のプラスチックの溶融によって形成されたプラスチック部品の表面の線形トレースですが、溶融物は交差点で完全に溶融していないため、1つに溶融することはできません。それらはほとんど直線であり、深いところから浅いところへと発達します。この現象は、外観や機械的特性に一定の影響を及ぼします。
(5)。リップル:射出成形部品の表面に渦巻きや雲のようなうねりがあるか、透明な製品の内部に波状のパターンがあります。これはリップルと呼ばれます。
(6)。オーバーエッジ(フラッシュ、ケープ)。
(7)。寸法の不一致:成形プロセスにおける射出成形部品の収縮と反り
2.品質管理と改善:技術と管理が含まれます
(1)。技術レベル:材料の正しい選択、製品構造の設計、適切な金型材料の選択、充填、排気、部品の取り外しを容易にするための金型構造設計の最適化、パーティング表面、流路、ゴム入口の合理的な設定。高度な射出成形装置またはプロセスの使用。
(2)。管理レベル:入荷する材料の品質管理、効果的な品質方針と基準の策定、技術トレーニング、合理的なプロセス仕様の策定、データの記録と分析、および音質システムの確立。
Mestech社は、年間数百の金型と数百万のプラスチック製品を国内および世界中の顧客向けに製造しています。 プラスチック射出成形の詳細や見積もりについては、今すぐお問い合わせください。